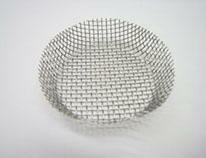
Role of Mesh in Low-Pressure Casting Process
The mesh plays a crucial role in the low-pressure casting process. It is a type of filter used when injecting molten metal into the mold, serving the following functions:
- Impurity Removal: Captures impurities and oxides in the molten metal, improving product quality.
- Flow Uniformity: Streamlines the flow of molten metal, preventing casting defects.
- Gas Discharge: Effectively releases gases contained in the molten metal, preventing defects caused by bubbles.
- Backflow Prevention: Prevents the molten metal that has filled the mold from flowing back, thus maintaining casting quality.
These functions make the mesh an essential element for producing high-quality cast products.
Low-Pressure Casting Process
Low-pressure casting is a casting method where molten metal is injected into the mold at low pressure. The process is as follows:
- Mold Preparation: First, the mold is appropriately prepared. The mesh is pre-installed in the mold.
- Molten Metal Preparation: Next, the metal is melted to prepare the molten metal. The molten metal is usually injected into the mold at a low pressure of about 0.1 to 1.0 bar.
- Injection and Solidification: The molten metal flows uniformly into the mold and solidifies within it. During this process, the mesh removes impurities and improves quality.
- Product Removal: Once solidification is complete, the mold is opened, and the product is removed. Post-processing is performed on the product as needed.
Low-pressure casting is suitable for manufacturing high-precision, complex-shaped products.
Products Manufactured by Low-Pressure Casting
Low-pressure casting is widely used to manufacture high-quality and durable products such as automotive aluminum wheels. Representative products include:
- Automotive Aluminum Wheels: Lightweight, high strength, and high design flexibility.
- Engine Components: Parts requiring high precision and heat resistance, specifically cylinder heads and cylinder blocks.
- Aircraft Components: Structural components of aircraft where weight reduction is crucial.
- Household Appliance Parts: Parts that combine aesthetics and functionality.
These products are manufactured by leveraging the characteristics of low-pressure casting, meeting demands for quality and performance.
Low-pressure casting is utilized in various fields due to its precision and quality. Recently, research on new materials and processes to reduce environmental impact has been progressing, expanding the scope of low-pressure casting applications. Ongoing technological innovations in low-pressure casting are expected to enable the production of even higher quality and more diverse products. For any questions or consultations regarding the mesh essential for low-pressure casting, please contact TWC.
The mesh plays a crucial role in the low-pressure casting process. It is a type of filter used when injecting molten metal into the mold, serving the following functions:
- Impurity Removal: Captures impurities and oxides in the molten metal, improving product quality.
- Flow Uniformity: Streamlines the flow of molten metal, preventing casting defects.
- Gas Discharge: Effectively releases gases contained in the molten metal, preventing defects caused by bubbles.
- Backflow Prevention: Prevents the molten metal that has filled the mold from flowing back, thus maintaining casting quality.
These functions make the mesh an essential element for producing high-quality cast products.
Low-Pressure Casting Process
Low-pressure casting is a casting method where molten metal is injected into the mold at low pressure. The process is as follows:
- Mold Preparation: First, the mold is appropriately prepared. The mesh is pre-installed in the mold.
- Molten Metal Preparation: Next, the metal is melted to prepare the molten metal. The molten metal is usually injected into the mold at a low pressure of about 0.1 to 1.0 bar.
- Injection and Solidification: The molten metal flows uniformly into the mold and solidifies within it. During this process, the mesh removes impurities and improves quality.
- Product Removal: Once solidification is complete, the mold is opened, and the product is removed. Post-processing is performed on the product as needed.
Low-pressure casting is suitable for manufacturing high-precision, complex-shaped products.
Products Manufactured by Low-Pressure Casting
Low-pressure casting is widely used to manufacture high-quality and durable products such as automotive aluminum wheels. Representative products include:
- Automotive Aluminum Wheels: Lightweight, high strength, and high design flexibility.
- Engine Components: Parts requiring high precision and heat resistance, specifically cylinder heads and cylinder blocks.
- Aircraft Components: Structural components of aircraft where weight reduction is crucial.
- Household Appliance Parts: Parts that combine aesthetics and functionality.
These products are manufactured by leveraging the characteristics of low-pressure casting, meeting demands for quality and performance.
Low-pressure casting is utilized in various fields due to its precision and quality. Recently, research on new materials and processes to reduce environmental impact has been progressing, expanding the scope of low-pressure casting applications. Ongoing technological innovations in low-pressure casting are expected to enable the production of even higher quality and more diverse products. For any questions or consultations regarding the mesh essential for low-pressure casting, please contact TWC.