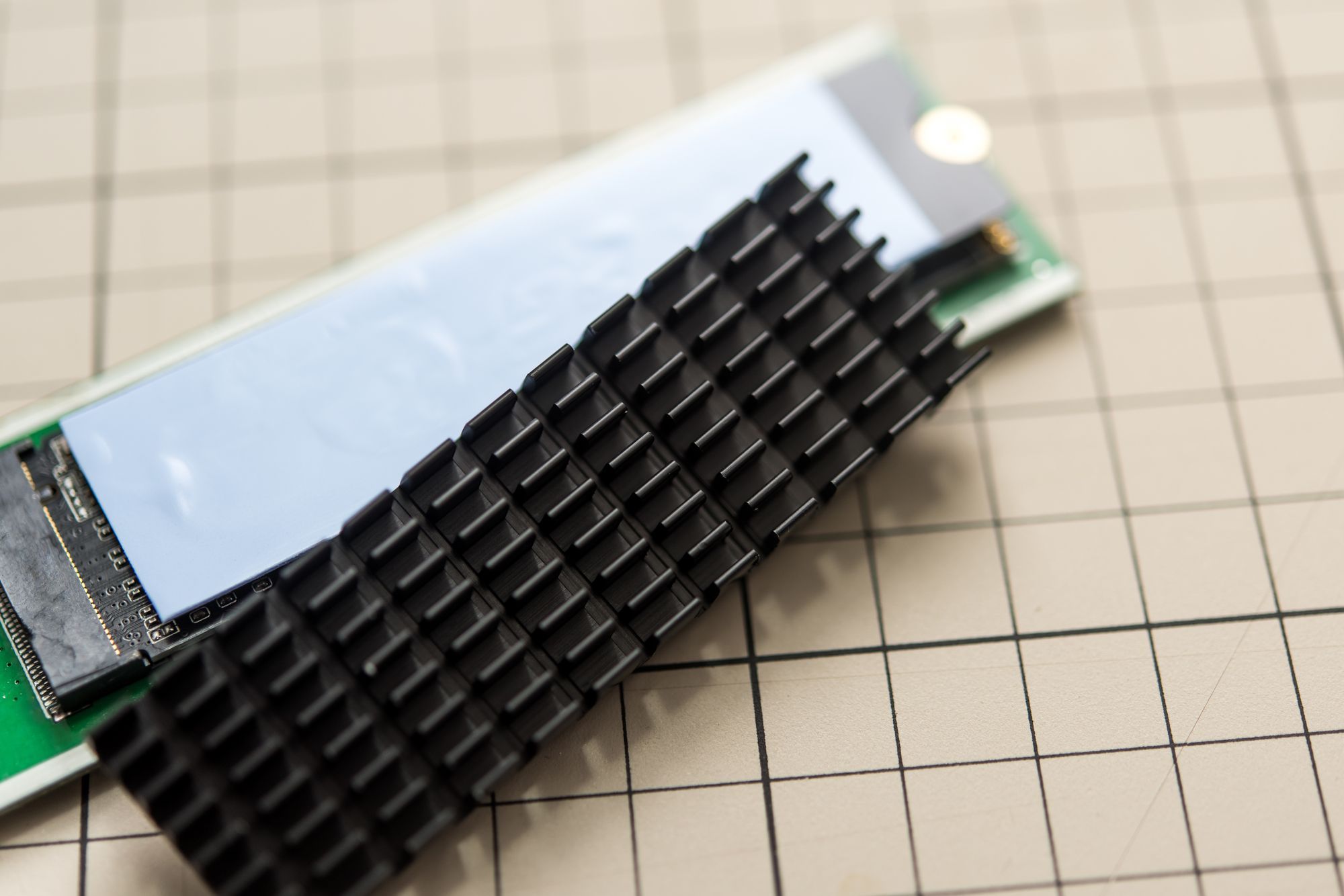
Thermal Conductivity and Thermal Impedance | Thermal Characteristics for TIM Selection
As semiconductor packages in electronic devices become highly integrated, countermeasures against heat generation have become essential. The most common means of thermal management is to transfer heat to heat dissipators, such as heat spreaders and heat sinks. A TIM (Thermal Interface Material) is essential to efficiently transfer the heat generated by semiconductor chips.
When using or selecting a TIM, basic knowledge of thermal characteristics is necessary. In this section, thermal conductivity and thermal impedance are explained, and then the TIM types and their workability are introduced.
Characteristics of TIMs
When reducing the heat generated by electronic components, heat is generally dissipated by conducting the heat to heat dissipation materials, such as heat spreaders, heat sinks, and external housings. The TIM is mounted between the semiconductor chip, which is the heat source, and the heat dissipation material.
Purpose of TIMs
If a heating element is in direct contact with a heat dissipator, even though at the macro level it appears to be in contact, at the micro level there will be an air gap at the interface due to fine surface irregularities. Since air gaps have very low thermal conductivity, heat from the heating element is transferred only at the points where there is no air gap, resulting in inefficient heat dissipation. To solve this problem, TIM must be used to fill the air gap and efficiently transmit heat.
TIM should be selected by considering the material and surface shape of the heating element and the heat dissipator, and by focusing not only on the thermal conductivity characteristics but also on flexibility and workability.
Thermal conductivity and thermal impedance
The first thing to focus on in TIM selection is the thermal properties related to heat transmission. An understanding of thermal conductivity and thermal impedance is essential.
Thermal conductivity
Heat can only be transferred from areas with higher temperatures to areas with lower temperatures by conduction, convection, or radiation, and not the other way around (second law of thermodynamics). The thermal energy transferred through a material can be calculated using Fourier's equation.
Thermal conductivity is a material-specific value that expresses the ease with which heat is transferred. The higher the thermal conductivity of a material, the faster the heat propagates and thus the greater the cooling effect.
Thermal impedance
In addition to thermal conductivity, thermal resistance is another indicator of a material's thermal properties. Thermal resistance is calculated by the following formula.
When thermal conductivity is constant, thermal resistance depends on the thickness of the material and the area of heat transfer where the materials are in contact with each other.
However, if there is a contact interface where the material surface has fine irregularities that form an air gap, there will be resistance to heat flow at the contact surface between the materials. The total resistance (thermal impedance), which is the sum of the thermal resistance of the material itself and the thermal resistance generated at the interface of contact between the materials, should be considered.Thermal impedance is the total thermal resistance to the flow of heat from the surface of the hot part to the surface of the cold part. Therefore, the thermal impedance θ is calculated as follows.
Thermal analysis and evaluation are necessary for TIM selection
To reduce thermal resistance at the contact interface, TIM must have high thermal conductivity in the thickness direction as well as the flexibility to fill air gaps.
Thermal conductivity is described in catalog specifications for TIM. However, since thermal conductivity is a material-specific value, actual thermal design must consider thermal impedance including thermal resistance at the contact interface.
The heat transfer coefficient cannot be converted to thermal impedance. Also, thermal impedance varies depending on the state of fine irregularities at the interface. Actual equipment evaluation and simulation are indispensable for thermal management using TIM.
TIM types and workability
In mass production, the use of TIMs to reduce thermal impedance requires not only thermal conduction performance, but also the ability to minimize variation during TIM installation and fill irregularities on the attachment surface. For this purpose, workability during TIM mounting is also important. This section introduces the TIM types and their workability.
TIM types
There are various types of TIM as shown in the table below, and the appropriate one should be selected according to the usage conditions.
TIM type | Characteristics |
Thermal grease |
|
Thermally conductive sheet (gap filler) |
|
Thermal gel |
|
PCM (Phase-Change Materials) |
|
Thermal tape |
|
High thermal conductivity adhesive |
|
Solder |
|
TIM workability
TIM has different workability depending on the product type. Also, if air gap removal is incomplete due to variations during TIM mounting, the thermal management may not be as effective as expected for the thermal conductivity.
Thermal grease, for example, has the advantage of high fluidity and easy thinning, but has the disadvantage of difficulty in applying evenly and poor workability. Thermally conductive sheets are excellent for use in areas with large steps and have high re-workability, but their relatively high hardness makes them ineffective for thermal management if the compression force is insufficient. Thus, the workability of TIM varies depending on the material, which affects the effectiveness of thermal management after mounting.
In addition, TIM materials may pump-out due to the heat cycle at the location of use, or dry out due to continuous use. Therefore, it is essential to evaluate TIM materials, including their workability, before use.
For more information about heat management, contact Taiyo Wire Cloth.
We utilize simulation technologies, measurement technologies, and other expertise in heat management to propose optimal solutions for our customers' designs. If you have concerns about heat management, please feel free to contact us.